Bearings are incredibly important to the operation of many machines. When a bearing is damaged or defective, everything grinds to a halt. We will be detailing the most common reasons a bearing may fail, what to look for, and how to fix it. For stainless steel ball bearings that you can count on, look to HCH Bearing Americas. We’ll keep everything running smoothly.
HCH BEARING
DEEP GROOVE BALL BEARING MANUFACTURER
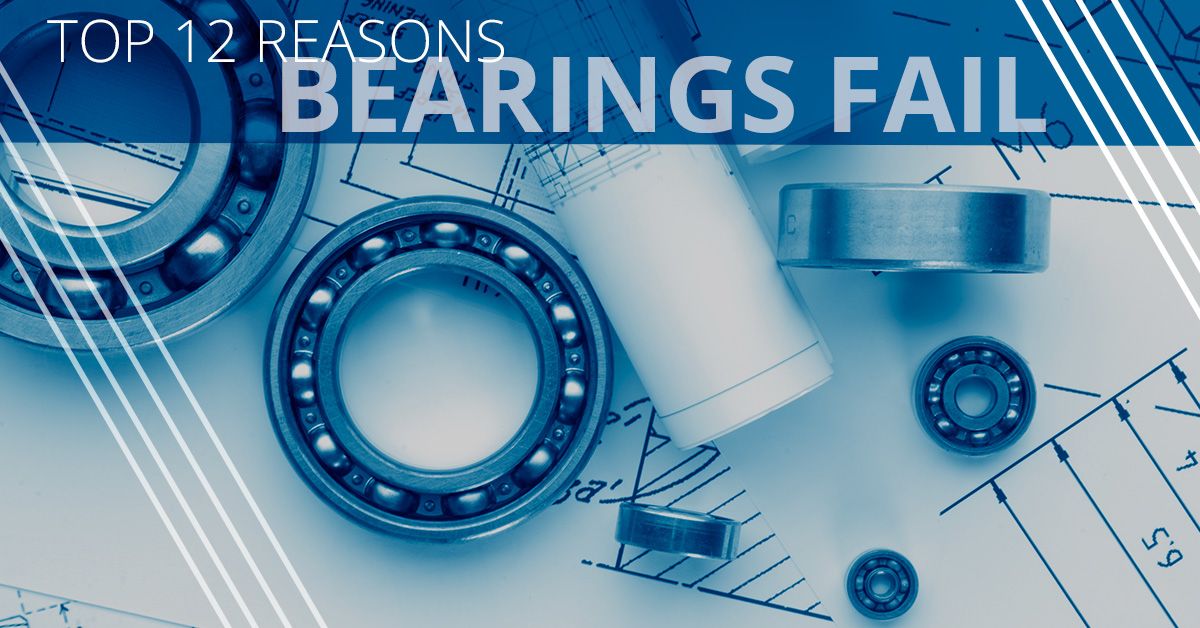
Top 12 Reasons Bearings Fail
-Improper Lubrication
A recent study reports that up to 80 percent of bearing failures are caused by improper lubrication. This can mean insufficient lubrication, use of incorrect lubricants, or excessively hot temperatures degrading the lubricant.
What to look for:
You’ll notice discolored rolling elements and rolling element tracks, typically blue or brown, along with overheating or excessive wear in the bearing.
Fixing it:
Apply the correct type and amount of lubricant, avoid loss of grease, and re-lubricate at the appropriate intervals.
-Contamination
When foreign substances come into contact with bearing lubricants or cleaning solutions, the bearing encounters contamination. Those foreign substances include dirt, abrasive grit, dust, steel chips from work areas, and dirty hands or tools.
What to look for:
Dented rolling elements and raceways, causing excessive vibration.
Fixing it:
Filter out the lubricant to clear it of foreign substances. Ensure your work areas, tools, fixtures, and hands are all clean to reduce the possibility of future contamination.
-Improper Mounting
Typically, bearings should be mounted with a press fit on the rotating ring.
What to look for:
There are many conditions that can cause denting, excessive wear, cracked rings, high operating temperatures, early fatigue, and the premature failure of bearings. This includes mounting bearings on shafts by applying pressure or blows to the outer race, mounting bearings into a housing by pushing on the inner ring, loose shaft fits, loose housing fits, overly tight fits, out-of-round housings, and a poor finish on the bearing seat.
Fixing it:
Always follow the proper mounting instructions. Ensure all employees are properly trained on proper mounting, as well as the difference between properly and improperly installed mounting.
-Misalignment
Many issues can cause misalignment of a bearing, including bent shafts, out-of-square shaft shoulders, out-of-square spacers, out-of-square clamping nuts, and improper installation due to loose fits. These issues can all result in overheating and separator failure.
What to look for:
If the wear path is not parallel to the raceway edges of the non-rotating ring, this is a clear sign of misalignment.
Preventing it:
Use precision-grade locknuts. Inspect the shafts and housings for runout of shoulders and bearing seats.
-False Brinelling
Brinelling is defined as the permanent indentation of a hard surface. As the balls in a raceway move rapidly while equipment is idle, lubrication is worn away. Additionally, a lack of rotation in the bearing prevents fresh lubrication from spreading. Both of these situations result in false brinelling.
What to look for:
Linear wear marks in the axial direction at the rolling-element pitch. No raised edges as opposed to marks that would appear due to improper mounting.
Fixing it:
Either eliminate or absorb any external vibration that could cause the balls to move. Use lubricants that contain anti-wear additives.
-Corrosion
Corrosion can be caused by moisture, acid, low-quality or broken-down grease, poor wrappings, and condensation from excessive changes in temperature. This can be incredibly abrasive to the finely finished surfaces of ball and roller bearings.
What to look for:
This can be identified by red and brown stains or deposits on rolling elements, raceways, or cages. You may also notice increased vibration, excessive wear, an increase in radial clearance, or the loss of the preload.
Fixing it:
Divert any corrosive fluids away from bearing areas to reduce the possibility of contamination. Choose integrally sealed bearings. Utilize external seals for especially harsh environments. Choose the right bearing material, such as stainless steel, if you are unable to avoid corrosive environments.
-Electrical Damage (Fluting)
Consistent passage of alternating or direct current. Even if it is a low current, electrical damage can still occur.
What to look for:
Marks of a brownish color, parallel to the axis on a predominant area of the raceway or covering the entire circumference of the raceway.
Fixing it:
Ground or use insulated bearings to prevent electrical currents from flowing through the bearing.
-Spalling (Fatigue)
Overloading, excessive preload, tight inner-ring fits, and using the bearing past its expected lifespan can all result in spalling.
What to look for:
You can identify fatigue by a fracture in the running surfaces and subsequent removal of small, discrete particles of material from the inner ring, outer ring, or rolling elements. Spalling progresses and spreads with continued operation. It is always accompanied by a noticeable increase in vibration and noise during operation.
Fixing it:
A bearing with spalling needs to be replaced. Consider a bearing with a greater calculated fatigue life, internal clearances, and proper shaft and housing recommendations.
-Overheating
Excessive operating temperatures and improper lubrication can result in overheating. When under high temperatures, grease can bleed (purging the oil), which reduces the efficiency of the lubricant. Elevated temperature conditions can create oxidation, which leads to the loss of lubricating oils from the grease. This leaves a dry, crusty soap that can cause the bearing to seize up. The hardness of the metal can also be reduced under higher temperatures, which results in early failure.
What to look for:
Overheating is typically identified by discoloration of the rings, rolling elements, and cages. In the most extreme cases, the bearing components will actually deform. High temperatures can also degrade or destroy the lubricant outright.
Fixing it:
Thermal or overload controls, adequate heat paths, and supplemental cooling are all good options to implement to avoid overheating.
-Excessive Loads
Putting too much load on a bearing not designed to handle that level of load is a common cause of failure.
What to look for:
Heaving rolling-element wear paths, evidence of overheating, and overall widespread signs of fatigue are all symptoms of excessive loads.
Fixing it:
Either reduce the load or choose a bearing designed for a greater capacity. Different bearings are more equipped for larger or lighter loads, so it is important you select the correct bearing for the job.
-Improper Storage and Handling
When bearings are stored improperly, they are exposed to dampness and dust. If bearings are stored in excessively high temperatures, the grease’s shelf life can be degraded (the grease manufacturer will have storage specifications you need to consult). If boxes are opened and wrappings are torn prematurely, it can let dirt in and expose the bearings to potentially corrosive elements.
What to look for:
Ensure storage areas are not excessively damp and temperatures are controlled to avoid rusting. Avoid leaving uncovered bearings in storage areas that are not controlled.
Fixing it:
Keep bearings in a dry area maintained at room temperature. Keep bearings covered at all times keep them clean in storage. Do not unwrap bearings away from the installation site to minimize the possibility of exposure to corrosive elements.
-Improper Fit
Excessive loading of the rolling element can cause a tight fit. Radial clearance at operating temperatures needs to be considered to prevent improper fitting. When the fits are too loose, micro-motion can occur between fitted parts.
What to look for:
A heavy rolling-element wear path in the bottom of the raceway, overheating, or an inner-ring axial crack are all symptoms of a tight fit. Fretting (generation of fine metal particles), which leaves a distinct brown coloring, is a sign of a loose fit. Noise and runout problems can be caused by wear at the fitting surfaces.
Fixing it:
Ensure the bearing has proper clearance to avoid fit issues. Always consult the manufacturer’s installation guide to ensure proper fitting. Avoid using bearings not designed for the intended use, as bearings are not “one-size-fits-all”.
When you understand the issues that can cause a bearing to fail and what signs to be aware of, you are more equipped to limit equipment failures. Preventative maintenance will extend the lifespan of the bearing and help you avoid failures that derail productivity. When you are able to keep bearings at peak performance for as long as possible, you save your business both time and money. If your business is in need of high-quality stainless steel ball bearings, look no further than HCH Bearing Americas. With two plants in the U.S. (Elk Grove, IL and Jacksonville, FL), you’ll get your shipment quickly with the quality you can depend on. We hope to hear from you soon.